Hallo
Heute will ich Euch die Fertigung des Zierkranzes zeigen, eine wie ich finde sehr schöne Arbeit.
Grundlage ist die Kontur des Oberschrankes, wie sich einige erinnern, ein L-Profil mit einem 170mm Radius in der Schenkelecke.
Ich musste nun eine Lösung finden, die einmal den Radius-Bereich ermöglicht und dazu eine Lösung für die geraden Leisten, sinnvoll wäre es dann, wenn die Radien möglichst mit dem selben Werkzeug gefertigt werden.
Ich will versuchen mit meinen vorhandenen Mitteln auszukommen, nach einigen Überlegungen hatte ich dann Vorstellungen wie es gehen könnte und brachte diese zu Papier.
Bild 1
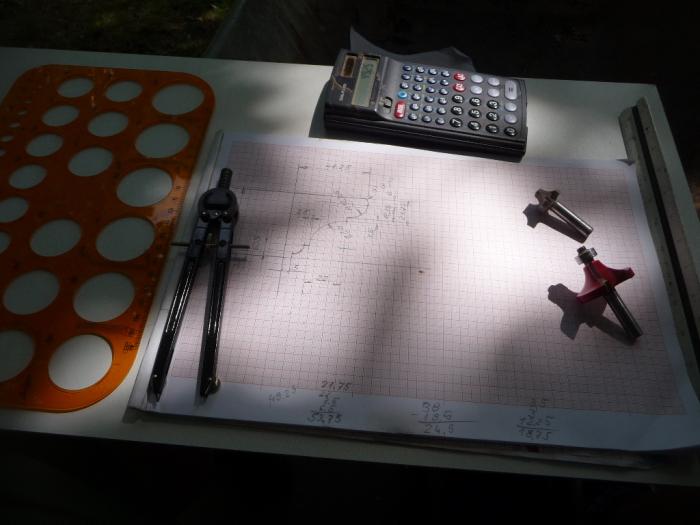
Ich hatte vor, mit dem Radius-Bereich anzufangen, also ein Rohling, zwei Segmente zusammen geleimt, ( um die Hirnholzflächen niedrig zu halten) den Rohling schraubte ich auf ein entsprechendes Leimholz 10mm dick, im Zentrum eine 8mm Bohrung, den Abstand zur Mitte dem 170mm Radius entsprechend.
Ich nahm dann mein Kopier-Holz das ich mit entsprechenden Details ausgerüstet habe, dieses Mal benutzte ich nur die Zentrierung mit einem 8mm Zylinderstift auf der darunter liegenden Platte.
Und los ging es mit dem fräsen, ich schwenkte immer mit Spanabnahme vor, leer zurück, aufpassen musste ich, würde ich von der falschen Seite mal bei fahren, könnte es zu Crash kommen, war aber leicht zu schaffen.
Hier seht man die groben Vorarbeiten.
Bild 2
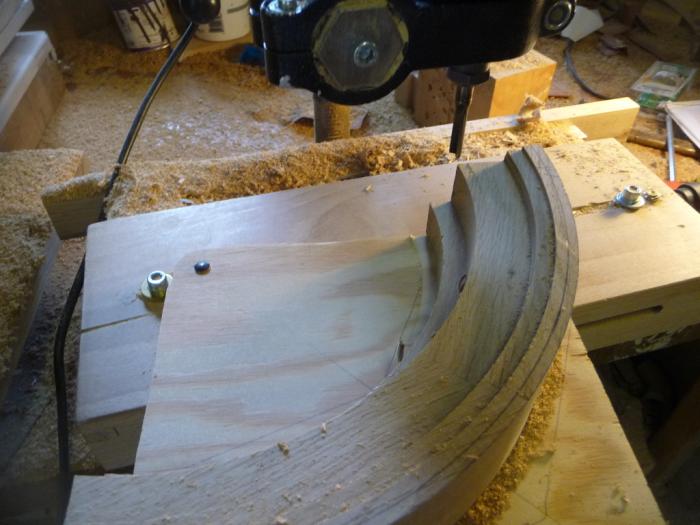
Ich ging daran mit einem Radiusfräser R¼, dem ich mal schon vor längerer Zeit den Zapfen für den Anlaufring entfernt hatte, einen entsprechenden Radius anzubringen, die beiden dazu gehörigen Flächen fertigte ich mit einem 8mm Zylinderfräser.
Bild 3
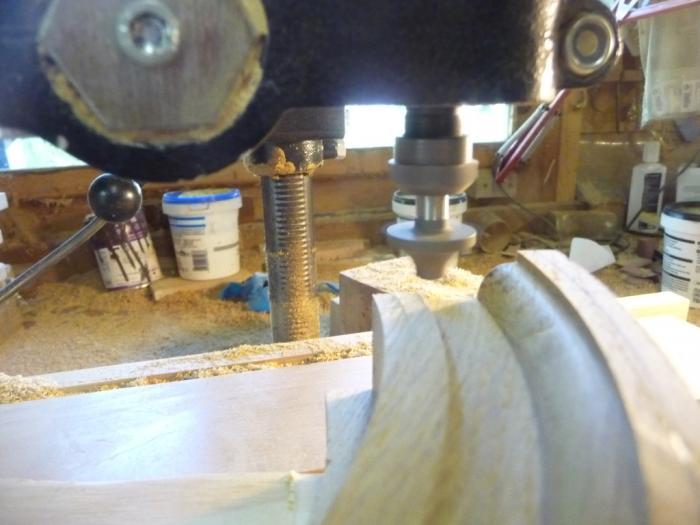
Dann kam Radiusfräser R 12,4mm mit Anlaufring zum Einsatz, der Anlaufring hätte ich auch abmontieren können, so diente er mir zu leichteren Einstellung, ich fuhr mit dem Wabeco-Schlitten so lange vor, bis das Kugellager Kontakt hatte und hatte so die richtige Einstellung.
Bild 3

Einen weiteren Radius fertigte ich mit einem Radiusfräser R¼, dem ich mal schon vor längerer Zeit den Zapfen für den Anlaufring entfernt hatte, die beiden dazu gehörigen Flächen fertigte ich mit einem 8mm Zylinderfräser.
Bild 4
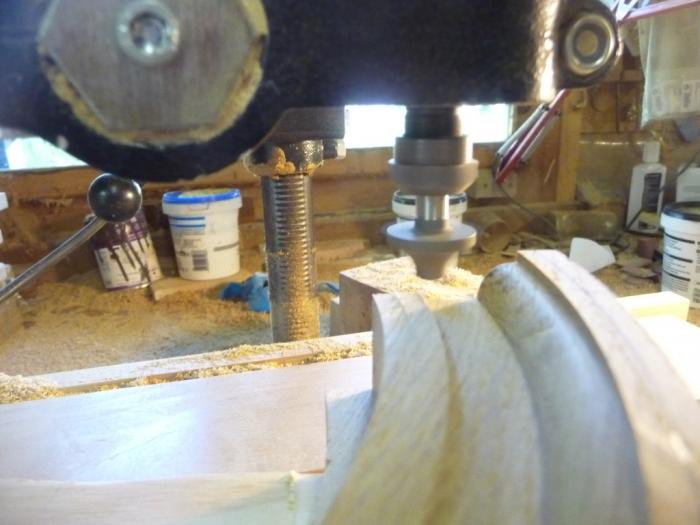
Dann kam der Halbrundfräser mit R ½ zum Einsatz, da der Radius kleiner als meine gewünschte R22mm musste ich mehrere Stiche machen, bei genauem Hinsehen sieht man die Übergänge, mit der Ziehklinge sind solche kleinen Erhöhungen schnell entfernt.
Bild 5
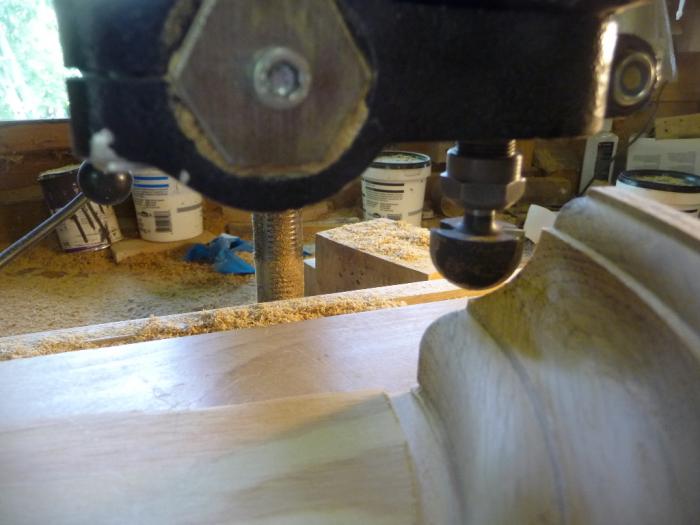
Das Segment ist nun fertig, ich beließ es aber noch auf seiner Aufspannplatte.
Bild 6
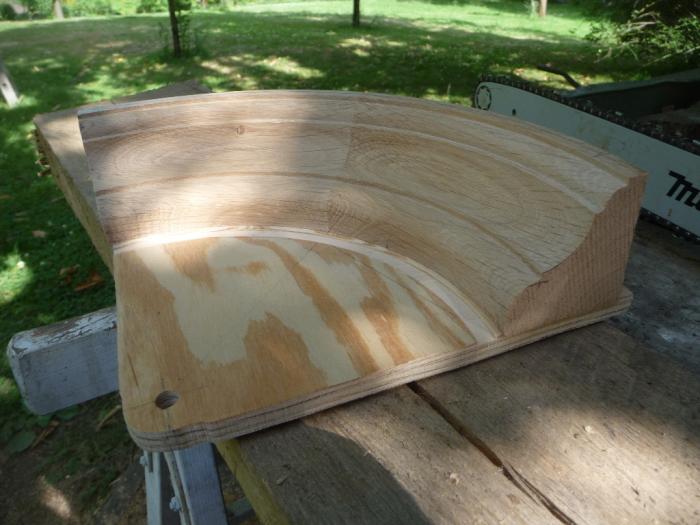
Eine nähere Aufnahme zeigt das Profil.
Bild 7
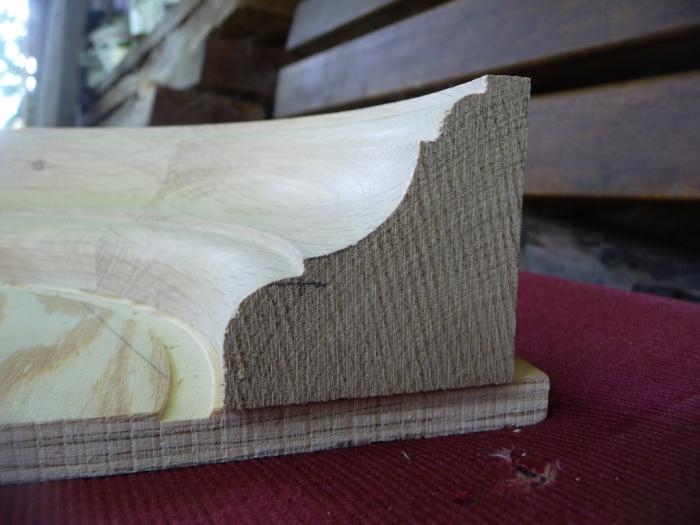
Nun traf ich die Vorbereitungen für die geraden Leisten, das wären eine lange Leiste 2.2m lang und drei kürzere, dazu eine Reservestück, sollte was schief laufen .
Um genau arbeiten zu können mussten die Teile einmal gleiche Abmessungen aufweisen und vor allem das lange Teil musste gerade sein, da ich es aus zwei Brettern zusammenleimte, schaffte ich mir eine Plane Unterlage, wozu ich einen alten Eichenbolen abrichtete, Krümmungen würden bei dem Profil Marken hinterlassen.
Bild 8
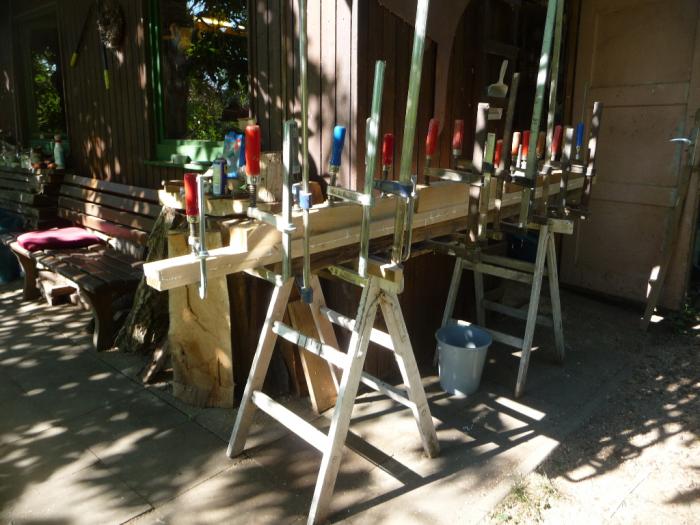
Während der Abbindezeit bereitete ich das Bogensegment vor, ich schnitt es analog dem Radius und dem Winkel (etwa 95°) sauber ab, das Trägerbrett hobelte ich soweit ab, bis es an der äußeren Kontur des Segmentes ab, um eine saubere Fläche zu erreichen führte ich das Teil über die Abrichte, die Messer hatte ich mit einer Hartmettalfeile etwas nachgeschärft, es reichte aus, um Ausreißer zu verhindern.
Bild 8
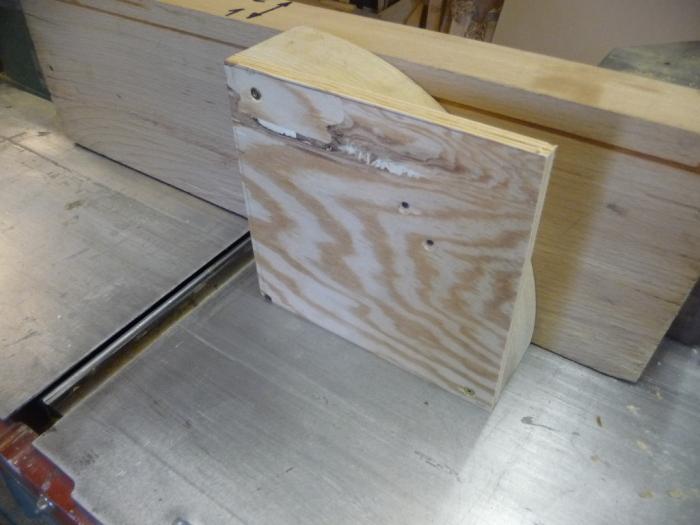
Nun ging ich hin und fräste in die neu geschaffene Fläche mit einem 5mm Nutfräser eine etwa 8mm tiefe Nut.
Bild 9
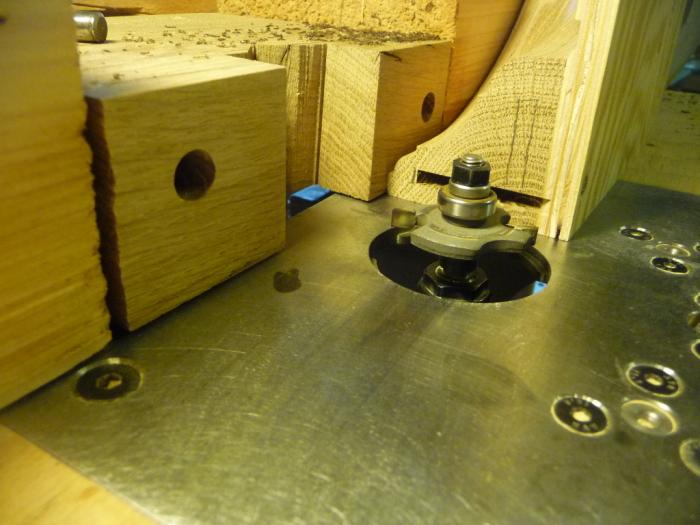
Nun erst entfernte ich das Trägerbrett und fräste an das Segmentteil eine zweite Nut, auch 5mm breit und 8mm tief.
Bild 10
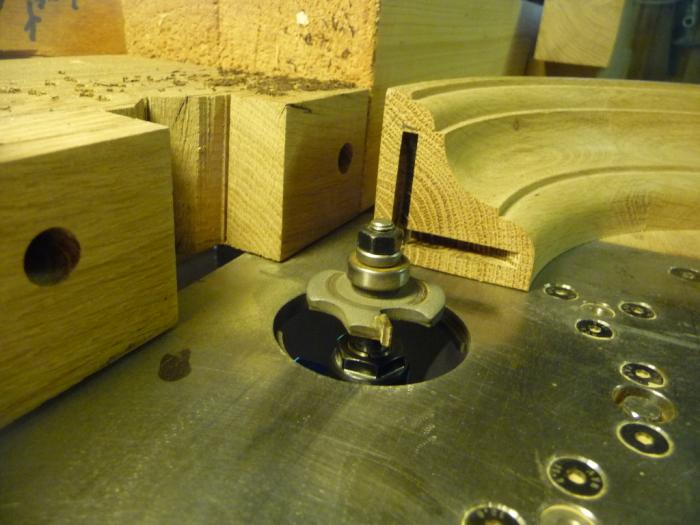
Inzwischen hatte ich die geraden Teile fertig gehobelt, wie ich schon sagte, genaue rechte Winkel und die Teile so gerade wie möglich.
An den an das Segmentteil anstoßenden Teile ( das Lange und ein kurzes) passte ich nun die entsprechenden Enden so an das Segment an, wie es im Endausbau von Nöten ist, deshalb umständlich, der Oberschrank steht unten im Haus, ich nahm mir vor die Gänge so gering wie möglich zu halten, wollte aber nicht so recht klappen, am Schluss hatte ich doch geschafft, die flächen stimmten.
In diese Flächen fräste ich nun auch die 5mm Nuten, auch wieder von Oben und Hinten.
Auf dem Bild kann das Ergebnis erkennen, steckte ich nun das Segmentteil und das dazu gehörige gerade Teil zusammen, so erreichte ich eine genaue Positionierung, die immer wieder wiederholen konnte.
Bild 11
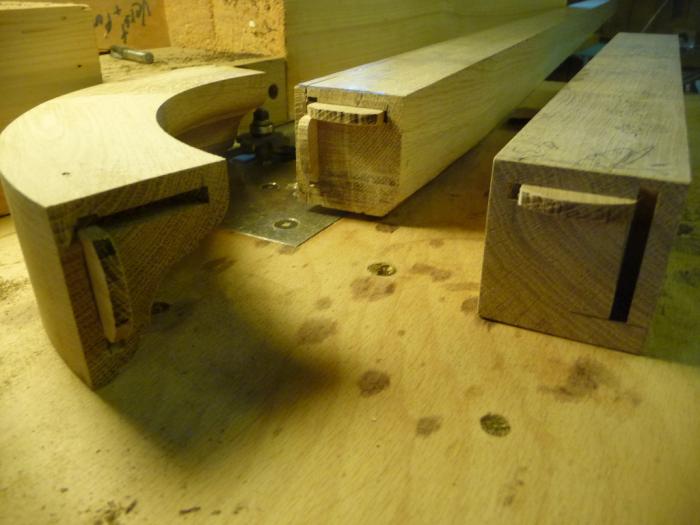
Ein Fehler in meiner Beschreibung, bevor ich die Trägerplatte entfernte fräste ich noch ein 4mm Durchgangsbohrung und dazu eine Freimachung, um eine Schraube eindrehen zu können.
Bild 12
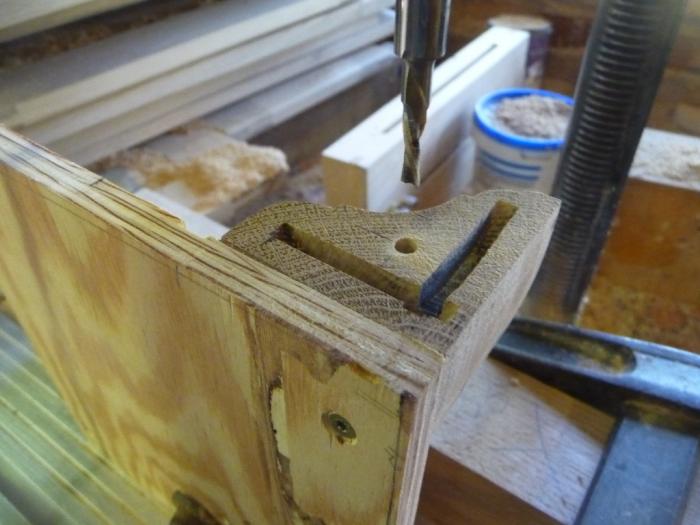
Die Freimachung an beiden Seiten.
Bild 13
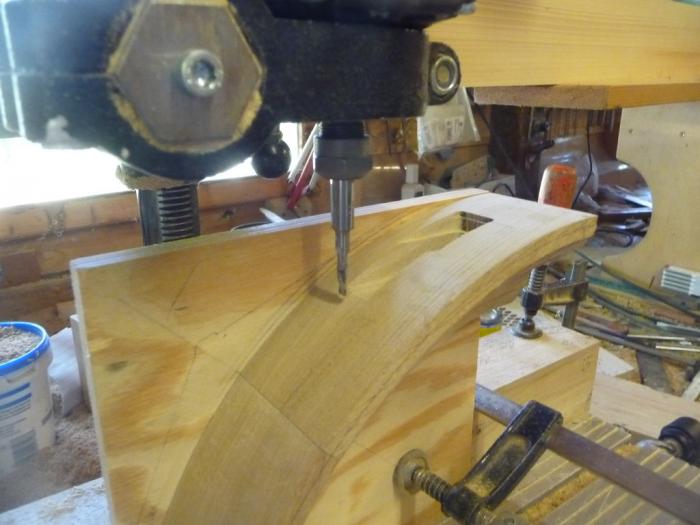
Nun konnte ich je eine Paarung zusammenstecken und mit spitzem Bleistift die Kontur abzeichnen.
Bild 14
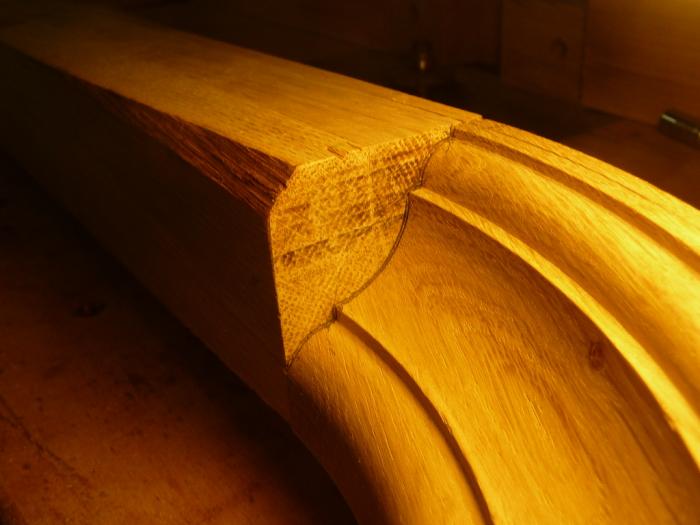
Nun kam eine schon alte Einrichtung zum Einsatz, praktisch eine Tischverlängerung, auf dem folgenden Bild kann man das Teil erkennen, es besteht aus einem kräftigen Balken, den ich etwa in der Mitte durchsägte, um dann die Trennstelle mit einer kräftigen Hartholz-Leiste wieder zusammen zu leimen, wobei ich in der Mitte einen Freiraum lies, um Fräswerkzeuge positionieren zu können, da die Lücke in meinem jetzigen Falle wesentlich kleiner sein konnte, spannte ich ein Füllstück mit zwei Schrauben ein.
Das Teil hängt bei mir immer an der Holzdecke, benutze ich es dann, richte ich es immer wieder neu ab, dieses mal etwas genauer.
Unter den kräftigen Balken schraube ich mir immer nach Bedarf Bretter an, die sind dann zwangsläufig auf Höhe des Tisches, wobei ich das Teil schon auf der Hobel, auf dem Frästisch und dieses mal auf dem Oberfräsentisch benutzt habe.
Da die zu fräsende Profile fast quadratisch waren, hatte ich am Anfang der Fräsarbeiten eine gute Positionierung der Werkstücke, später aber fräste ich mir die gute Führung weg, ich musste nun dafür sorgen, dass die Position erhalten bleibt, dazu schraubte ich eine Leiste auf die Verlängerung, die das Profil genau in Position hielt.
Was man auf dem Bild auch erkennte, ich schraubte mir ganz einfache Griffe auf die Werkstücke, um die den Vorschub möglichst ruckfrei tätigen zu können.
Bild 15
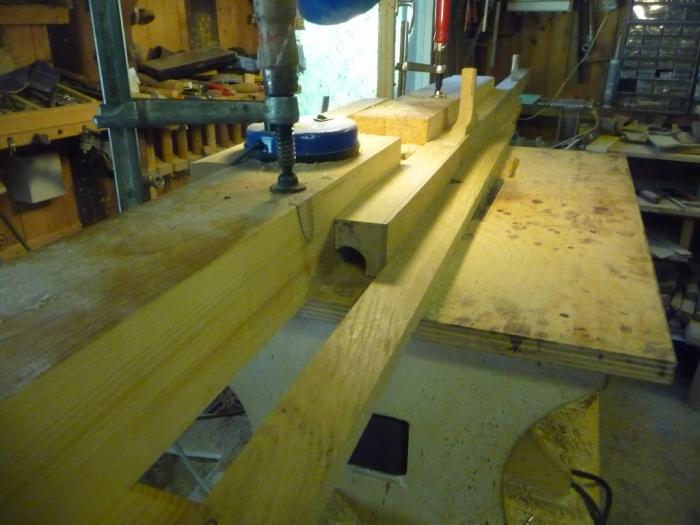
Was nun Folgt ist praktisch die Wiederholung der Arbeitsschritte wie beim Segment, ein Unterschied, ich benutze zum schruppen meinen Halbrundfräser, es macht einen großen Unterschied ob ich mit einem 8mm Fräser ins volle gehe, oder mit einem Halbrundfräser mit 1 Durchmesser, auch was ich schon oft sagte, der Halbrundfräser ist wesentlich gutmütiger als ein Zylinderfräser, zumal wenn er Rechtstrall hat, er neigt zum giftigen Zubiss.
Bild 16
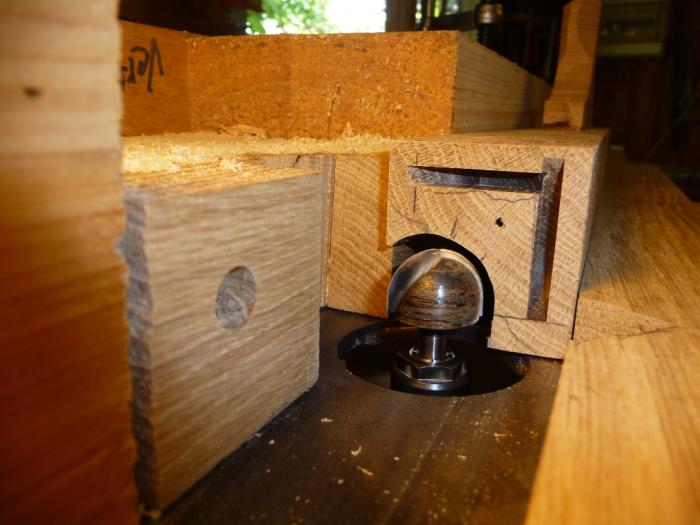
Bild 17
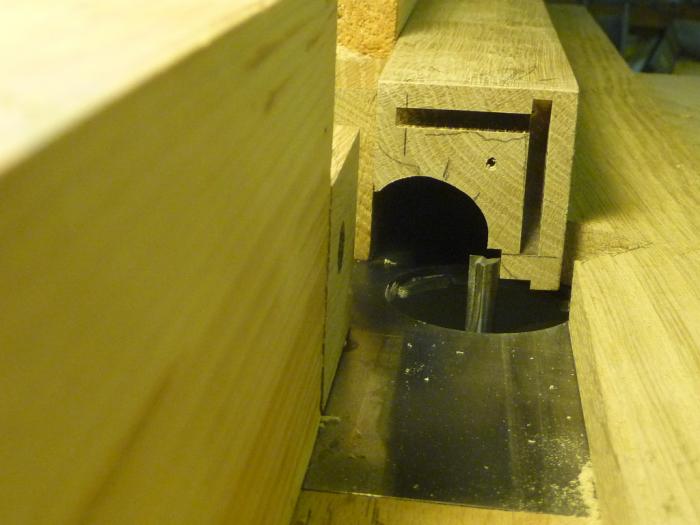
Bild 17
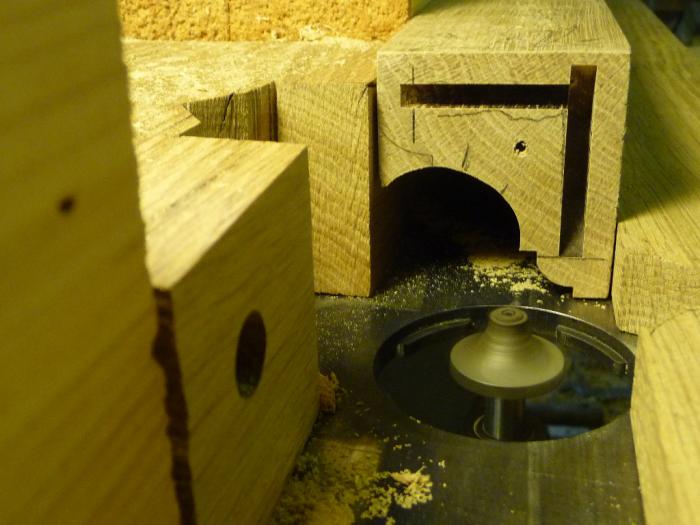
Bild 18
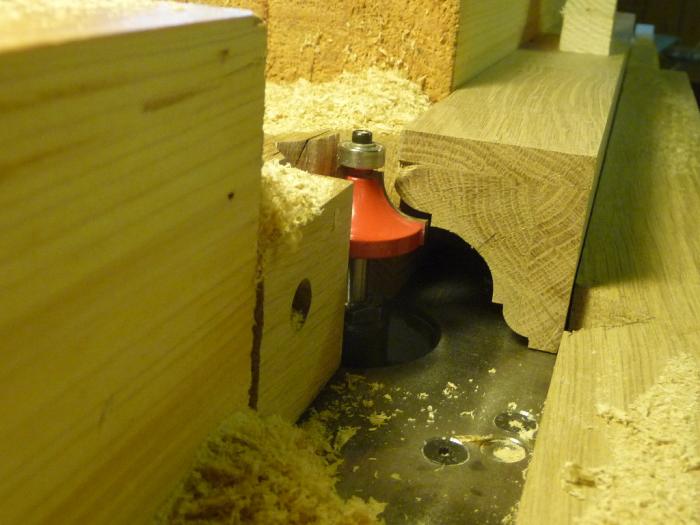
Was bei diesen Arbeiten sehr von nutzen war, ich konnte die Zustellung von unten tätigen, die einfache Tatsache, dass meine Spindel M12 unten und oben ein SW8 vorweist macht die Sache einfach.
Auf dem Bild erkennt man noch einen Schraubenkopf einer 6mm Inbus-Schraube, mit ihr Arretier ich den Schlitten, wobei ich großen Wert darauf legte an beiden Säulen zu arretieren, bei Klemmung auf einer Säule konnte ich immer wieder ungewollte Bewegungen feststellen.
Bild 19
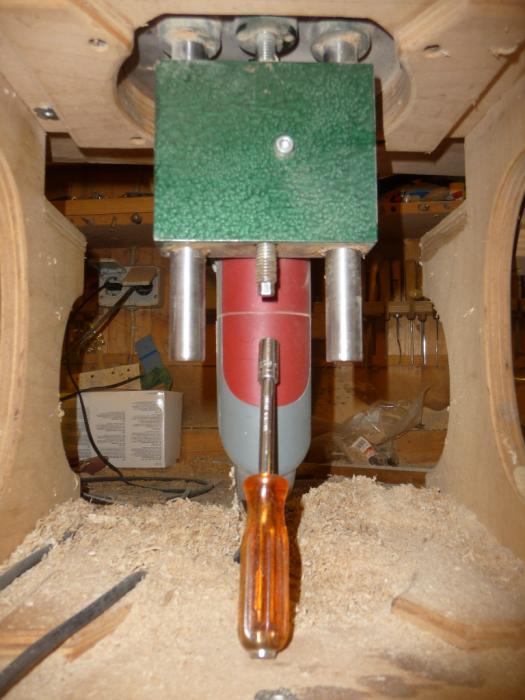
Als ich dann mit den Fräsarbeiten fertig war, schraubte ich die Teile zusammen, das Ergebnis war gut, die Teile passten gut zusammen, was auffiel, die Hitze am Freitag hinterließ einige Spuren, ich hab zum Glück keine schwitzende Hände, aber sauber waren die Teile nicht mehr, aber das Schleifen steht ja noch aus.
Hier die Schnittstelle aus der Nähe-
Bild 20
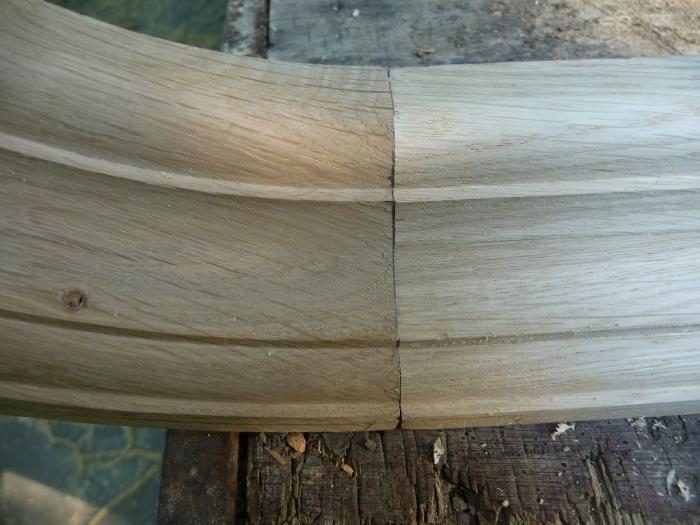
Das nächste was ich in Augenschein nahm war die Passgenauigkeit hin zum Korpus-Oberschrank, die Zierleiste soll 5mm überstehen und das stimmt so, ich könnte noch vor dem Verleimen durch leichte Korrekturen nachjustieren, scheint aber nicht notwendig.
Bild 21
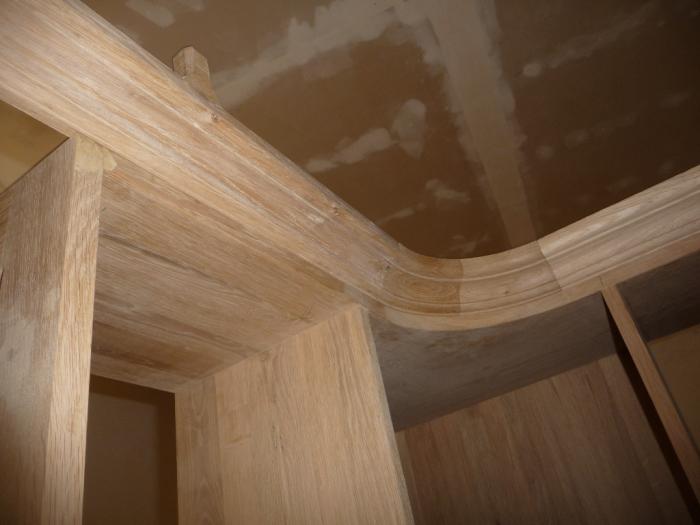
Auch ungeleimt macht das Teil einen stabilen Eindruck, die Arretierung der zwei Achsen ist, wie ich finde eine gute Sache.
Bild 22
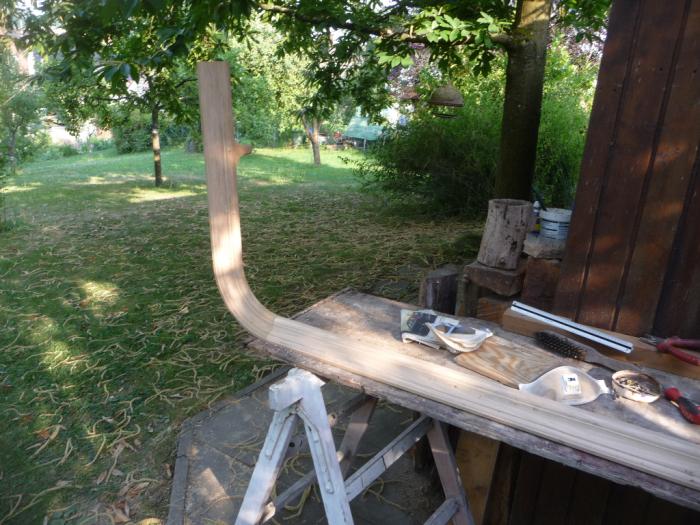
Noch ein Bild au der anderen Richtung.
Man kann die Schraube erkennen, ich nahm eine 3.5 mm dicke Schraube und bohrte zur Sicherheit mit einem 1.5mm Bohrer vor, sicher ist sicher, schlimm wenn mir die Schraube das Teil gespaltet hätte.
Bild 23
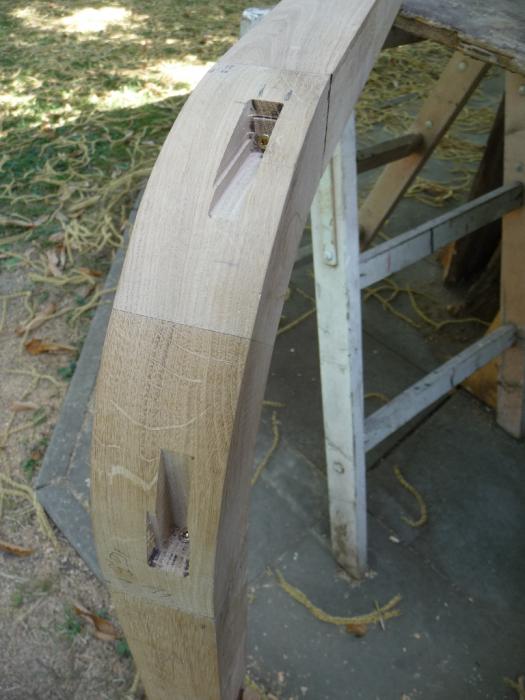
Abschließend, eine sehr schöne Arbeit, die richtigen Spaß machte.
Gruß Franz