Shoji-Paravent, mit Bildern
Verfasst: Fr 7. Mär 2008, 22:24
Hallo allerseits!
Ich möchte Euch mein jüngstes Projekt einen vierteiligen Shoji-Paravent vorstellen!
Der Paravent ist aus Kiefernholz gefertigt und ein Element hat die Abmessungen von 1550 x 480 mm.
Die Rahmenhölzer, Riegel (horizontal) und Sprossen (vertikal) sind quadratisch (26 x 26 mm). Die Kumiko (Leisten für die überblattete Versprossung) haben die Abmessung von 16 x 8,2 mm.
Ausgangsmaterial waren vorgehobelte Kiefernhölzer aus dem Handel (30 x 30 mm, bzw. 40 x 10 mm).
Grundlage für eine gute Shoji-Arbeit sind gerade Hölzer von gleichmäßiger Stärke. Aus diesem Grund ist Handelsware, auch wenn sie gehobelt ist, nicht direkt zu verarbeiten. Ich sehe den Vorteil dieser "fertigen" Ware darin, dass man das Holz besser beurteilen kann, als an einer rauhen Bohle davon abgesehen, dass man so eine Bohle auch aufsägen muß. Die Sache hat allerdings ihren Preis ca. 100 Euro für das Holz plus 48 Euro für die Paravent-Scharniere (bei uns in der Theater-Schreinerei; im Handel kosten 6 Stück 70 Euro).
Solch ein Paravent-Projekt scheint mir der ideale Einstieg in die Shoji-Technik zu sein: Nicht zu schwierig - aber alles was eine gute Shoji-Arbeit verlangt, ist hier schon gefordert. Wer gerne in aller Ruhe arbeitet und ein Genauigkeitsfreund ist, wird an dieser Arbeit seinen Spaß haben. Kreativität ist - zumindest auf diesem Shoji-Level - nicht so vonnöten!
Mit meinem Beitrag möchte ich allen Interessierten einen (kostenlosen) Einblick in die Shoji-Arbeit geben. Wer dadurch Lust auf eigenes Tun bekommt, dem empfehle ich die Bücher von Toshio Odate zu diesem Thema.
Es ist sehr schön, dass ein Mann wie Toshio Odate die handwerklichen Techniken die zum Bau einer Shoji nötig sind, mit seinen Büchern der breiten Öffentlichkeit zugänglich gemacht hat. Wer sich mit Shoji beschäftigen möchte, dem seien diese Bücher unbedingt angeraten!
Viele grundlegende Techniken und Vorgehensweisen kann man sich in seinem Buch "Shoji Schiebetüren Trennwände selbstgemacht" abschauen. Ich habe sie jedoch nicht sklavisch befolgt, sondern sie meiner Intuition folgend teilweise abgewandelt, so habe ich z.B. nicht die Kumiko-Überblattung verleimt, sondern die Kumiko-Zapfen in den Rahmenhölzern. An japanischen Werkzeugen kamen eine Universal-Dozuki und spezielle Shoji-Zwingen, sogenannte Hatagane zum Einsatz.
Abgesehen von einem Luftdruckkompressor (damit habe ich die Späne aus den engen Zapfenlöchern geblasen) kamen keine Elektrowerkzeuge zum Einsatz.
Zuerst möchte ich das Vorbereiten der Hölzer beschreiben.
Wer hier sauber und gewissenhaft arbeitet, legt die Grundlage für eine gelungene Arbeit!
Bild 1
Grobes Ablängen aller Hölzer mit der Gestellsäge auf dem Sägekreuz:
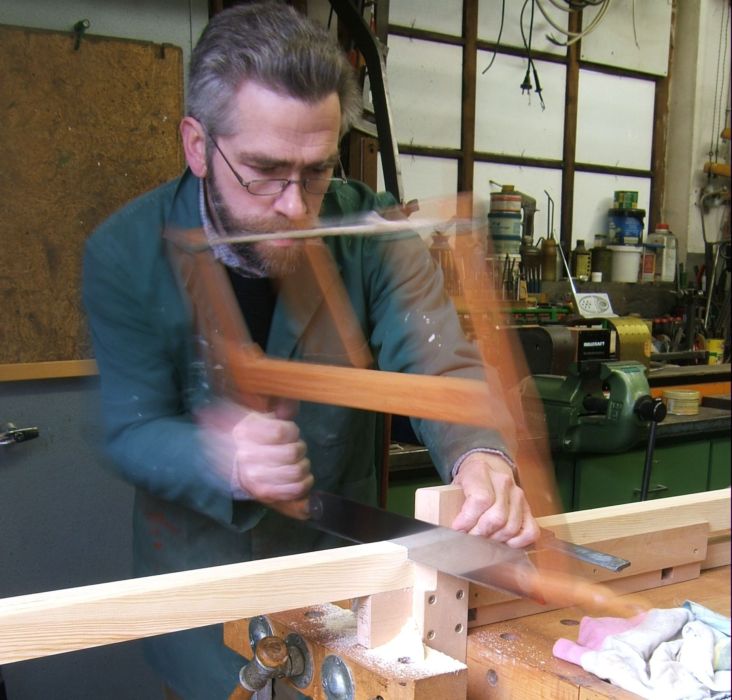
Bild 2
Abrichten der Rahmenhölzer:
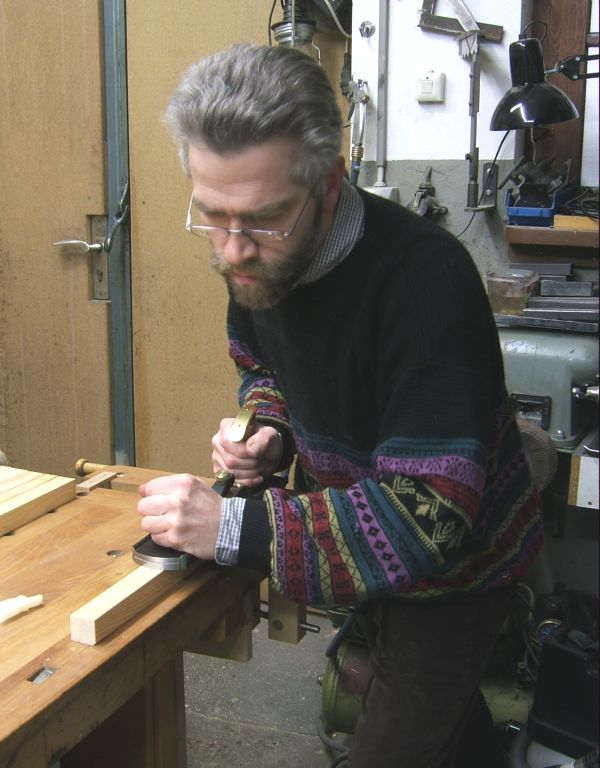
Bild 3
Vertikales Rahmenholz in der Fügelade. Die bereits abgerichtete Seite liegt unten; jetzt soll die Winkelkante angehobelt werden. Das abgebildete Holz ist rund. Die Rundung liegt mittig an, die "offenen Stellen" werden hinterlegt:
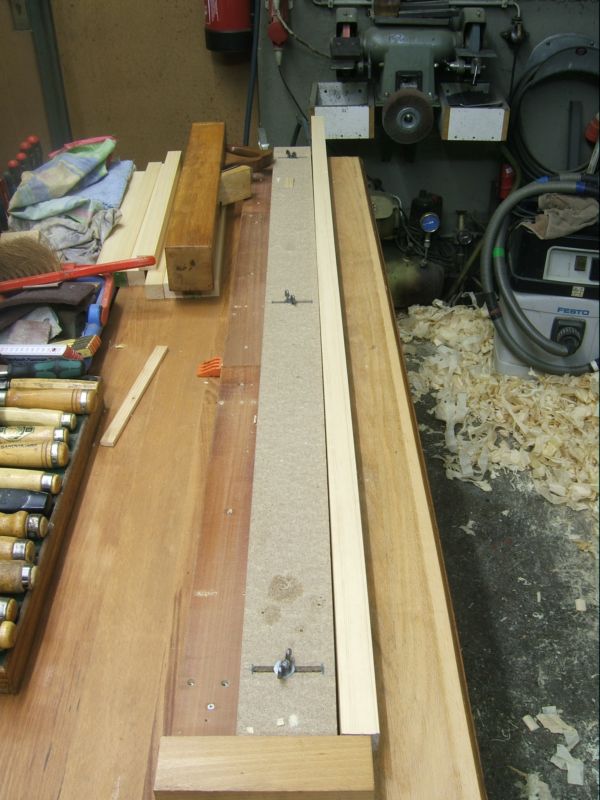
Bild 4
Hier die hinterlegten Stellen. Bei den dünnen Kumikos habe ich den Vertellmechanismus meiner Fügelade genutzt. Das Spanplattenbrett (das mit den Flügelschrauben) der Fügelade ist elastisch und lässt sich somit an ein rundes Holz anpassen:
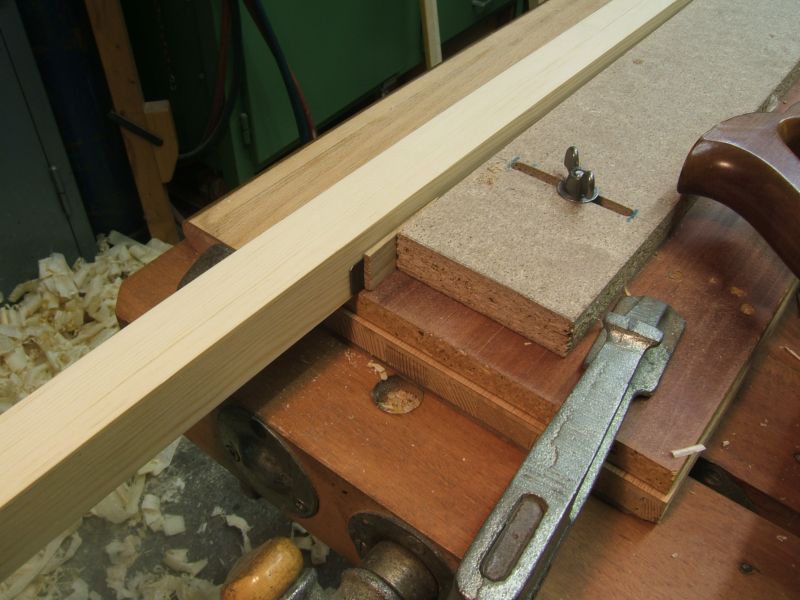
Bild 5
Mit einer rundgehobelten Latte wird Druck gemacht. Wichtig ist, dass die abgerichtete Seite beim Hobeln fest aufliegt und sich nicht etwa hochdrückt - sonst kann man hobeln bis kein Holz mehr da ist!
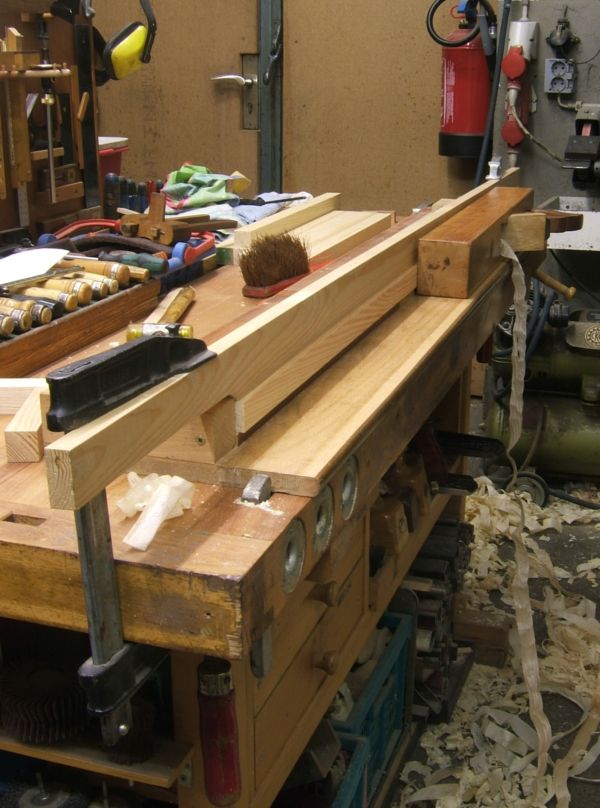
Bild 6
Ist die Winkelkante angehobelt, werden die Rahmenhölzer auf Dicke gehobelt. Um mir diese Arbeit zu erleichtern, habe ich meinen Stanley No. 6 mit dieser Zusatzeinrichtung versehen. Die grobe Vorarbeit habe ich mit einem alten Schlichthobel mit einer Spanabnahme von 3/10 mm gemacht (auf dem nächsten Bild hinten links):
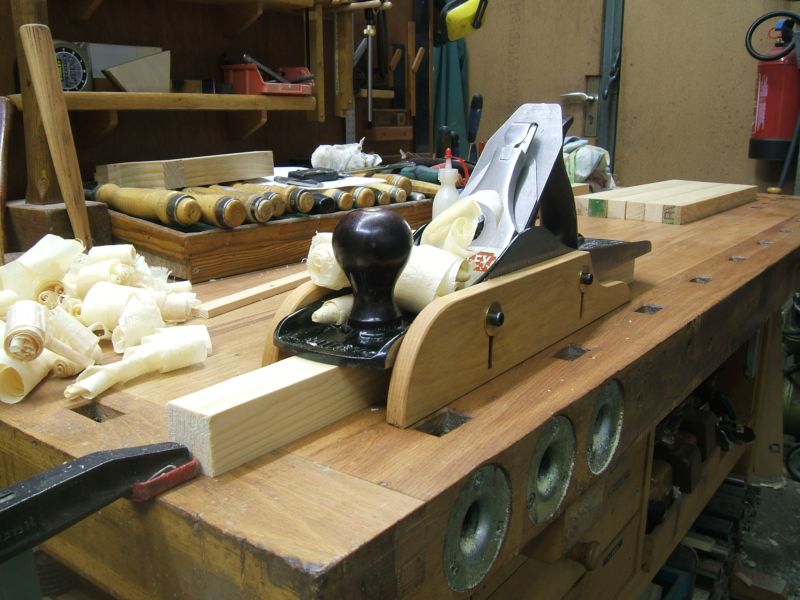
Bild 7
Überprüfen der Geradheit an einer geraden schmalen Kante:
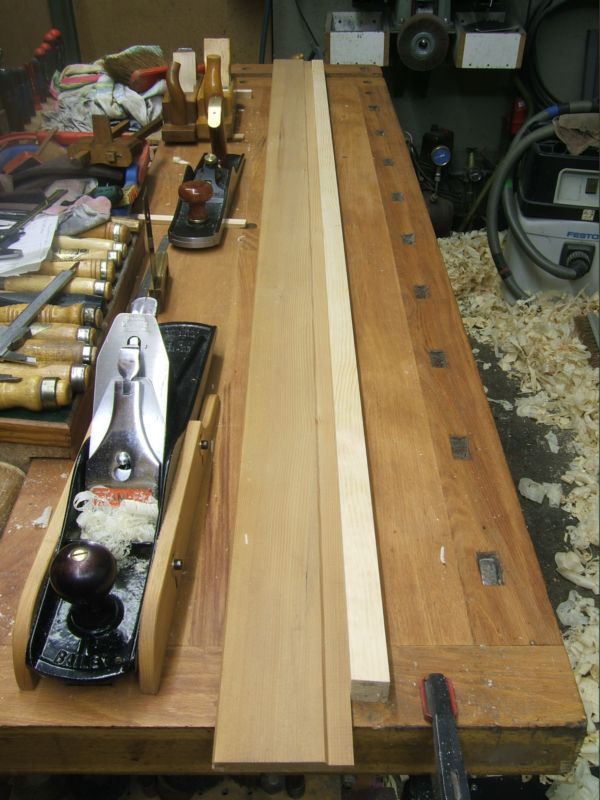
Bild 8
Bevor die Leiste (40x10) für die Kumikos aufgesägt wird, werden die Schmalseiten abgerichtet:

Bild 9
Aufsägen der Kumikos mit der Gestellsäge:
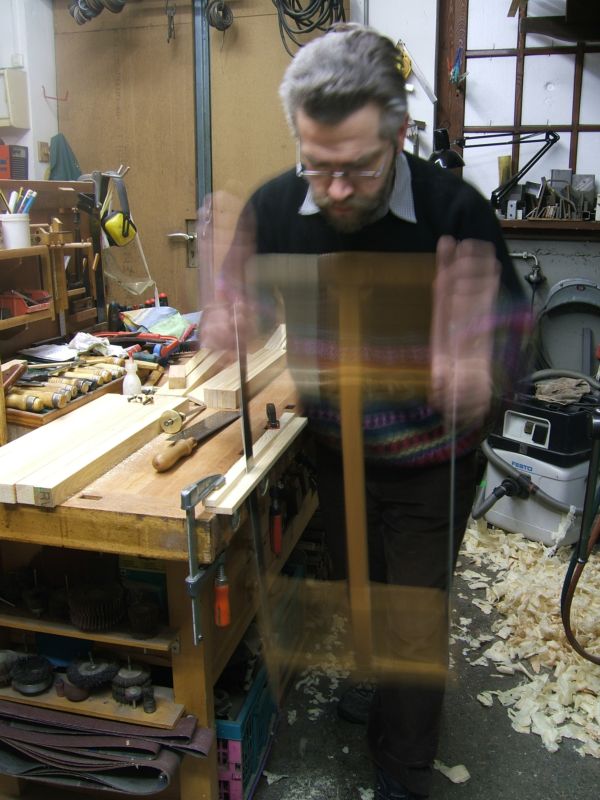
Bild 10
Dickenhobeln der Kumikos. Das Abrichten der dünnen Kumikos ist schwieriger als das der Rahmenhölzer, weil sie sich leichter durchbiegen. Am allerbesten wäre es, wenn man vor den Hobelarbeiten die Bank abrichtet, oder sich einen speziellen Hobelbalken herstellt:
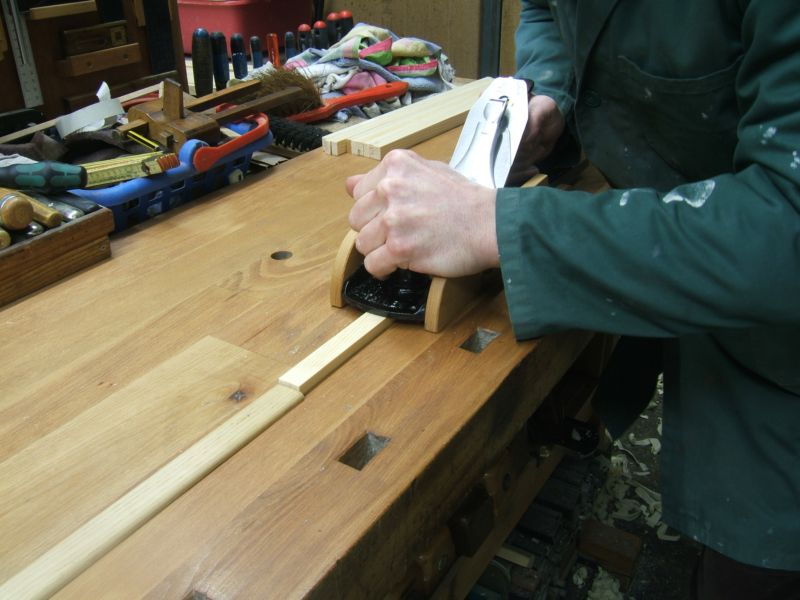
Hier im zweiten Teil möchte ich die Weiterverarbeitung der Hölzer und die Fertigstellung des Paravents darstellen.
Die weitere Grundlage für eine gelungene Arbeit bilden präzise Anrisse und deren Übertragung auf alle weiteren Teile. Ein Merkmal der Shoji-Verarbeitung ist das gemeinsame Anreißen und Bearbeiten der Einzelteile; so wurden z.B. alle 24 horizontalen (plus zwei Hilfs(Ersatz)-Kumikos) Kumikos zusammen angerissen und bearbeitet. Die Methode ist genial, hat aber den Nachteil, dass ein verrutschter Anriss, oder ein "versägter" Schnitt die ganze Arbeit ruinieren können!
Bild 11
Ansägen der Überblattung. Bei allen folgenden Sägearbeiten, habe ich immer mit einer Führungsrille für die Säge gearbeitet:
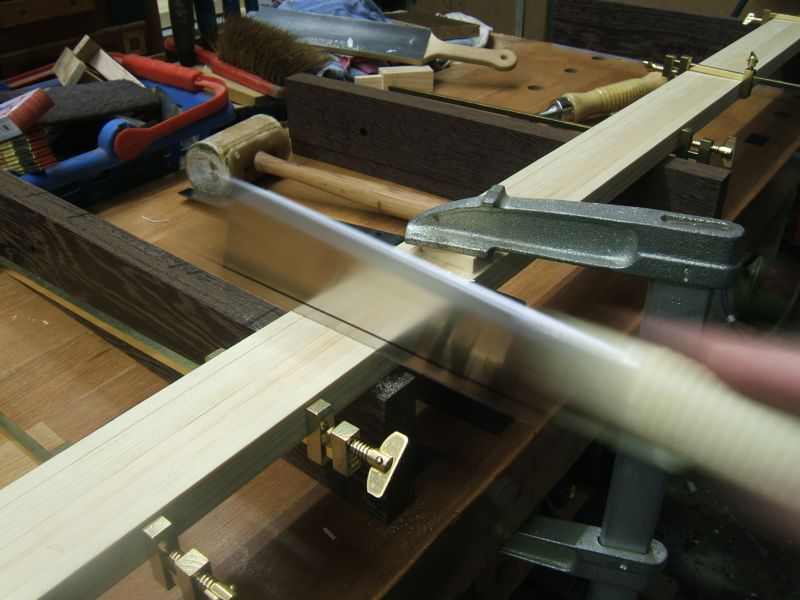
Bild 12
Sägen der Überblattung auf genaue Tiefe:
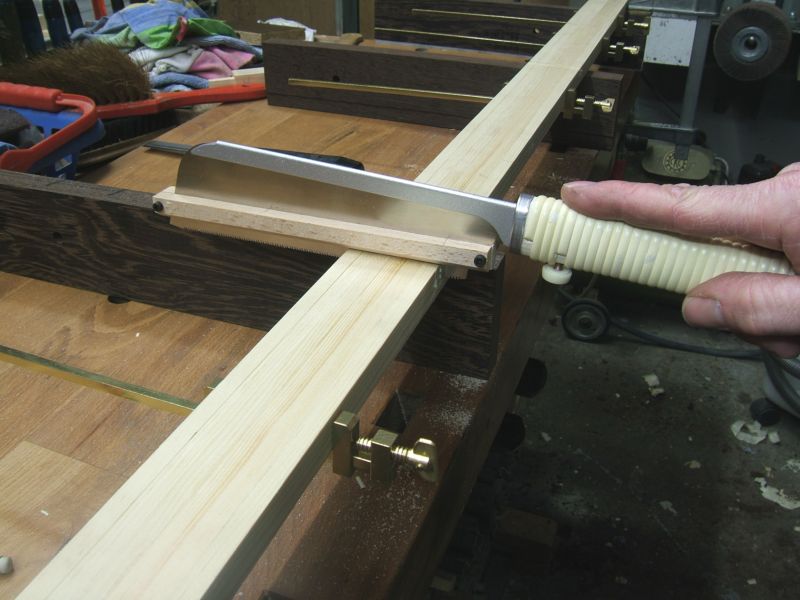
Bild 13
Überblattung teilweise ausgehoben:
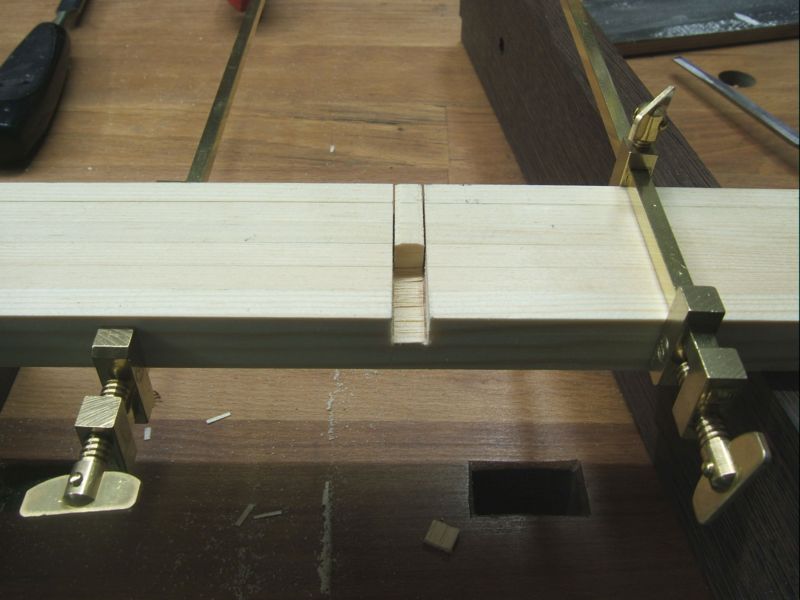
Bild 14
Ansägen der Kumiko-Zapfen:

Bild 15
Sägen der Kumiko-Zapfen auf genaue Tiefe:
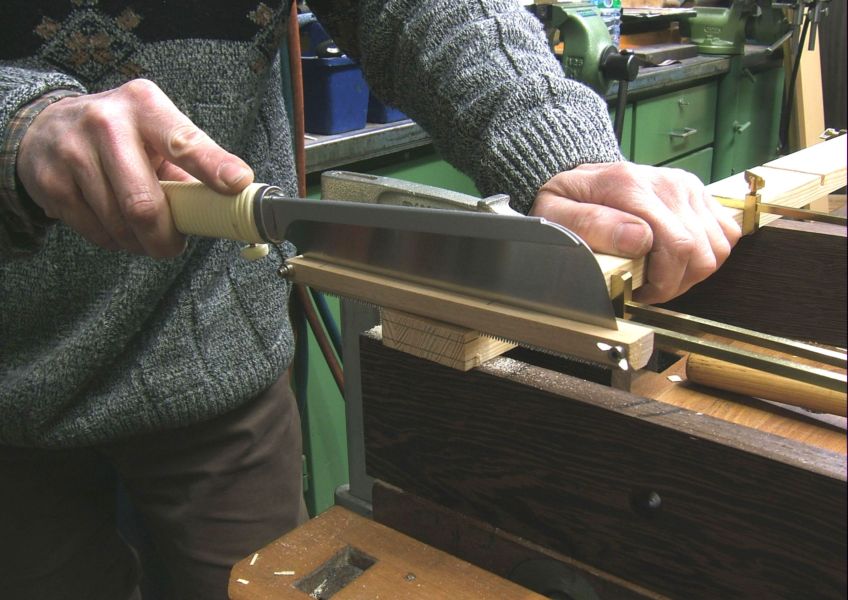
Bild 16
Grobes Vorarbeiten der Zapfen mit dem Stemmeisen:
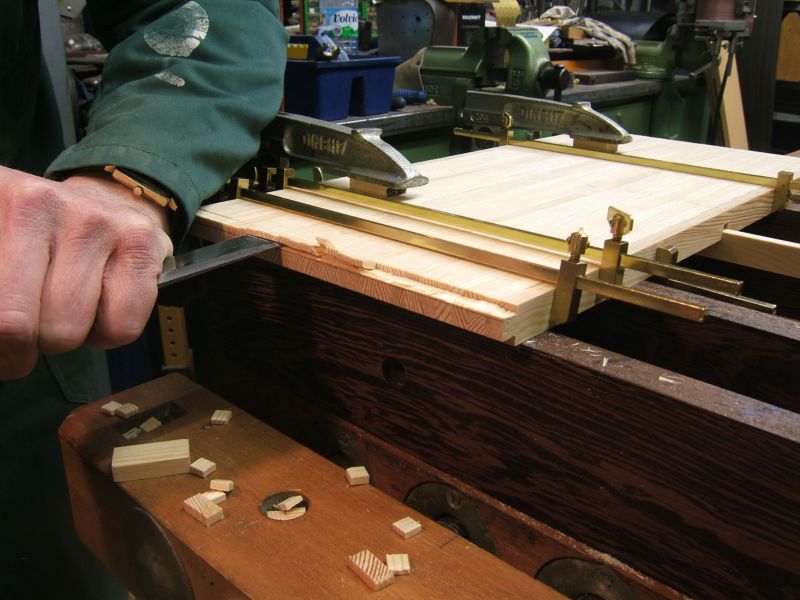
Bild 17
Fertigstellen der Zapfen mit dem Simshobel:
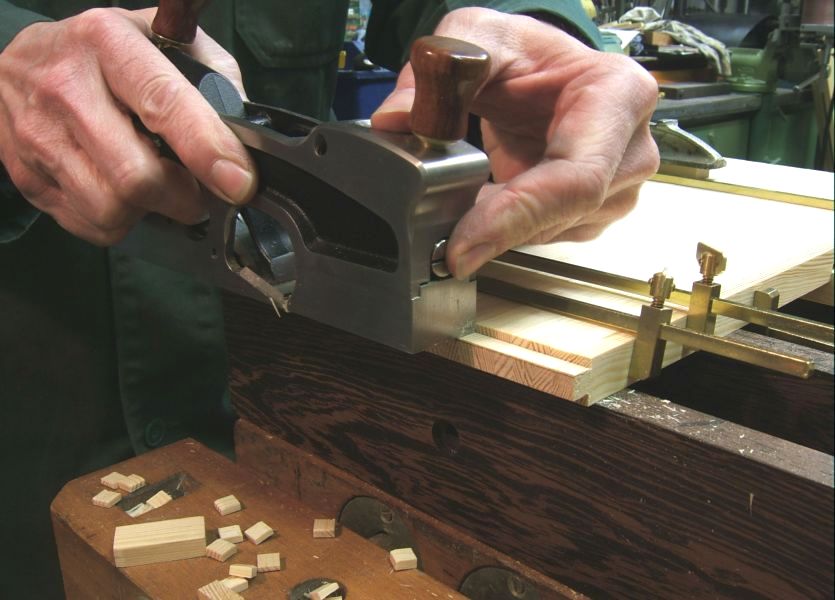
Bild 18
Prüfen der Zapfenstärke mit einer Leiste - in Kombination mit einem Meßschieber
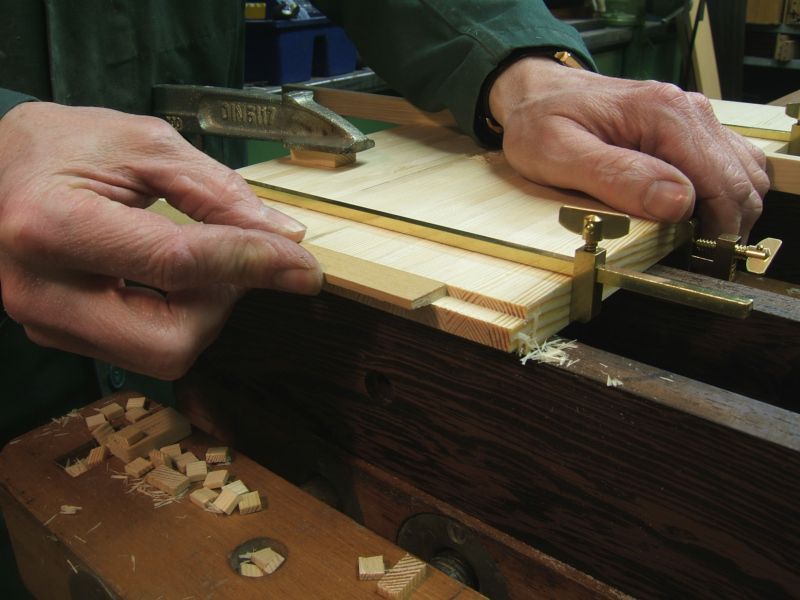
Bild 19
Anschrägen der Kumiko-Zapfen
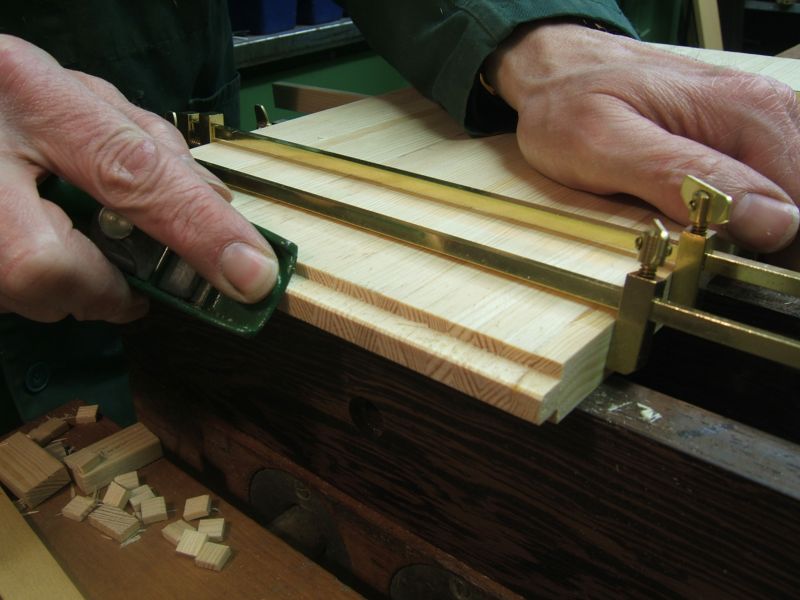
Bild 20
Anschrägen der Kumiko-Zapfen
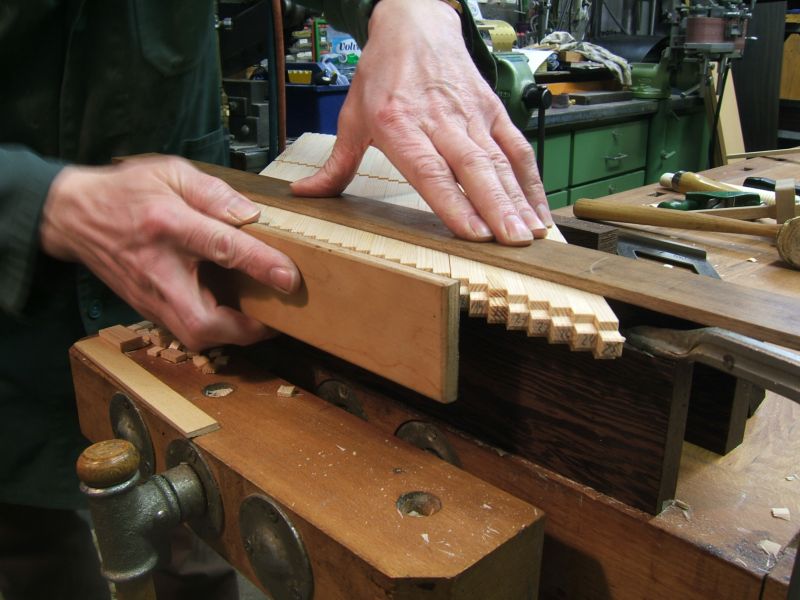
Bild 21
Anreißen der Zapfenlochhöhe für die Kumiko. Den Alu-Winkel hab' ich selbst gebaut. Der lange Schenkel hat die genaue Kumiko-Stärke (so habe ich mir einen teuren Adernschneider gespart). Ich habe die Zapfenlöcher nur partiell angerissen, weil man sichtbare Anrisse später nicht mehr wegbekommt:

Bild 22
Anreißen der Zapfenbreite mit meinem selbstgefertigten Zapfenstreichmaß (Vorlage war ein Zapfenstreichmaß von Dirk Böhmer):
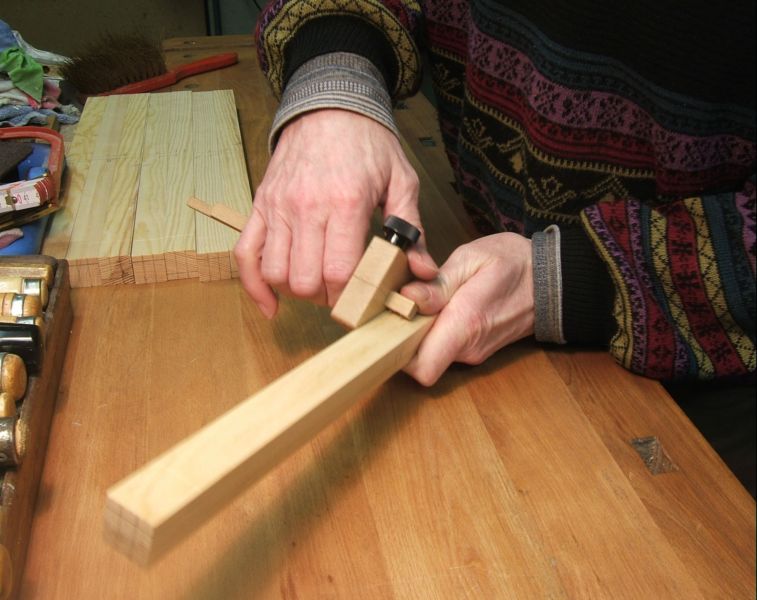
Bild 23
Hier wird das Zapfenloch gearbeitet. Mit der herkömmlichen Methode (funktioniert hier nur auf den ersten 4 mm) kommt man hier nicht weit. Von da an stemme ich alle vier Seiten und die Mitte, wie auf dem Bild ersichtlich. Wenn man schmale Stemmeisen direkt in den Riss setzt, wird das Zapfenloch größer als geplant - deswegen etwas vom Riß entfernt ansetzen. Sinngemäß werden auch die "großen" Zapfenlöcher für die Rahmenecken gearbeitet. Wichtig ist, das Eisen niemals an der Zapfenlochkante abzustützen um damit zu hebeln:
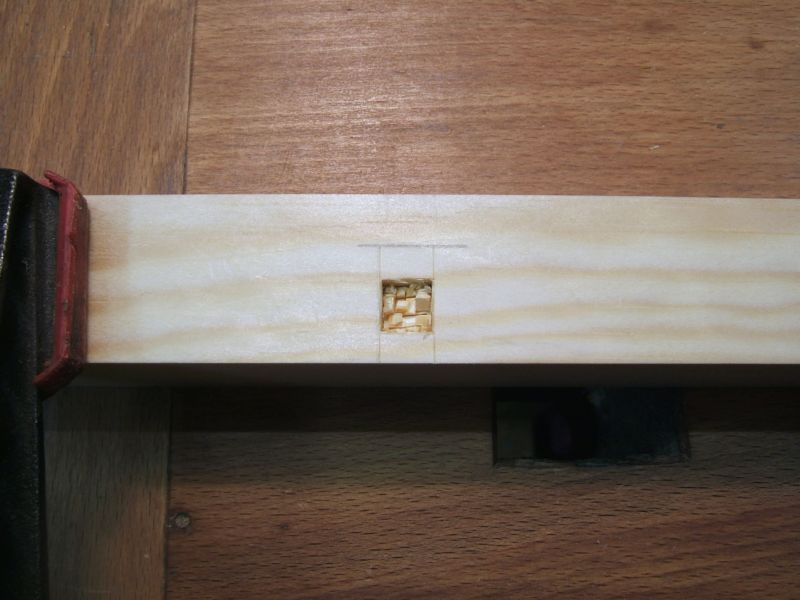
Bild 24
Dann löse ich die Späne indem ich mit einem 6er Stemmeisen kräftig drehende Bewegungen ausführe. Die gelösten Späne hab' ich mit Pressluft ausgeblasen. Die Japaner verwenden zu diesem Zweck ein spezielles hakenförmiges Stemmeisen:
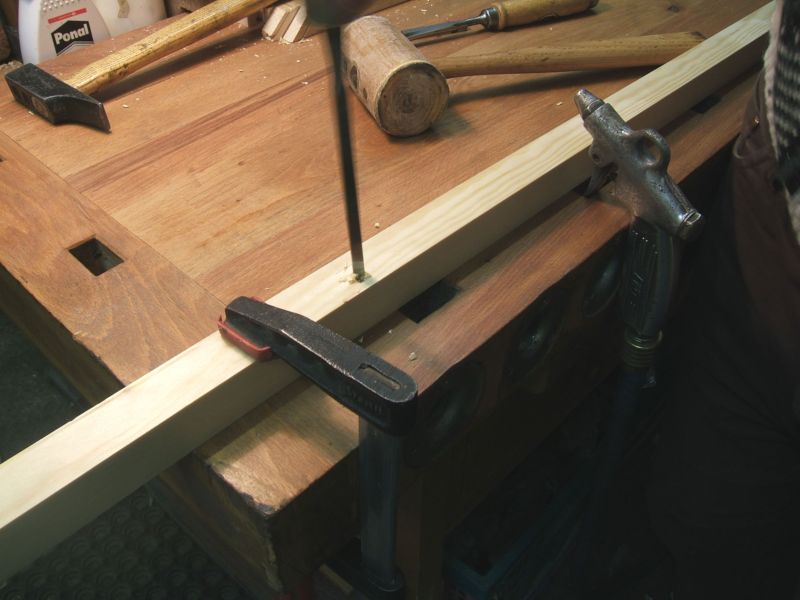
Bild 25
Sägen der Zapfenbrüstung für die horizontalen Rahmenhölzer:
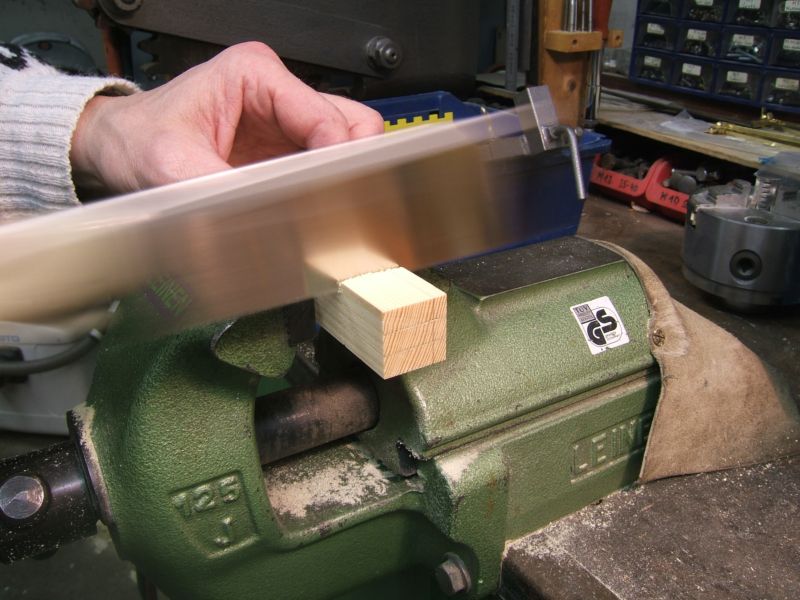
Bild 26
Längsschnitt und Brüstungsschnitt am Zapfen:
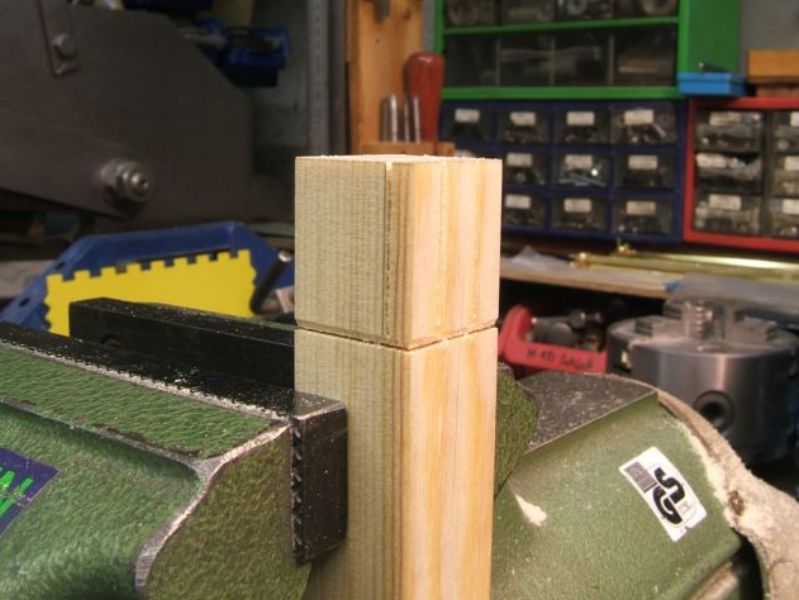
Bild 27
Säubern der vorgesägten Zapfen:
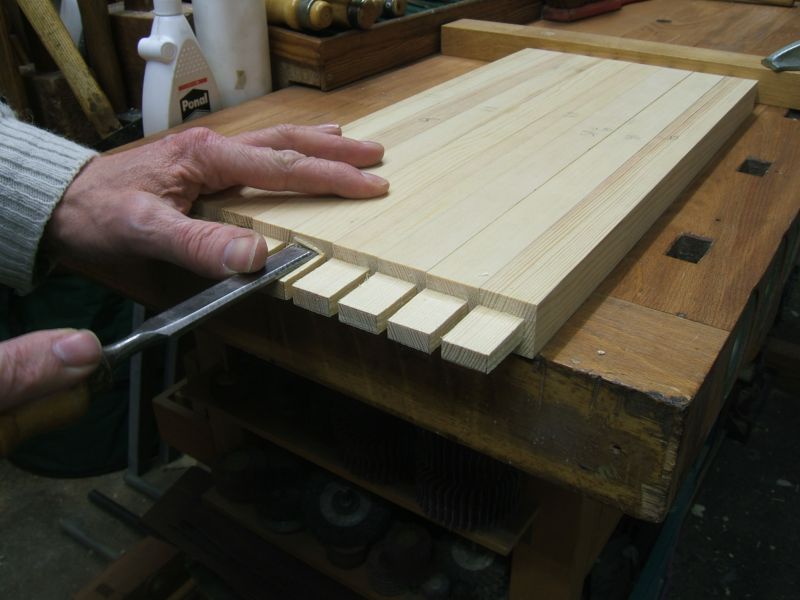
Bild 28
Hobeln der Zapfen mit dem großen Veritas Simshobel:
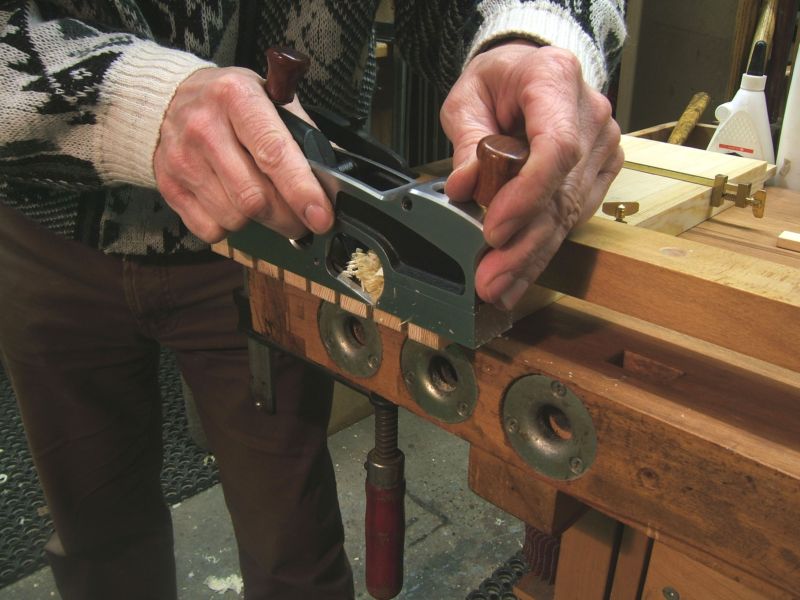
Bild 29
Genaues Ablängen der Zapfen:
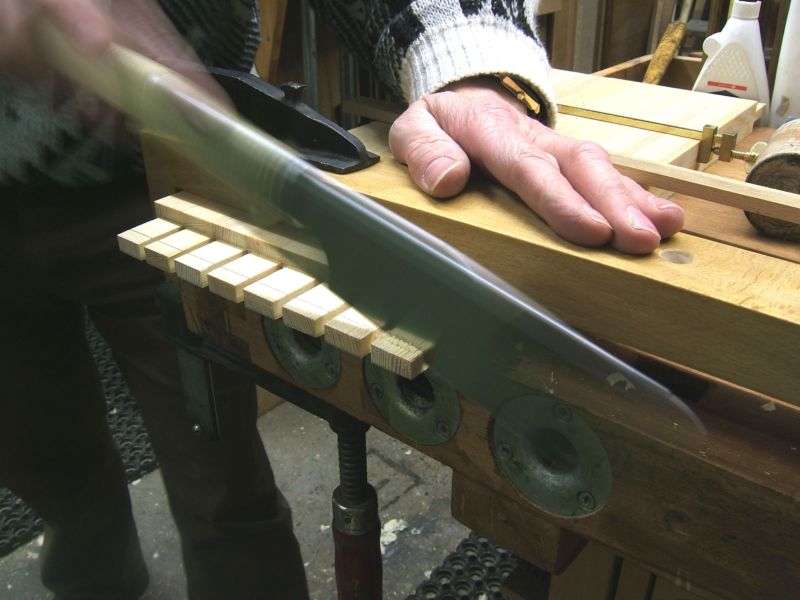
Bild 30
Die fertigen Hölzer vor dem Zusammenbau:
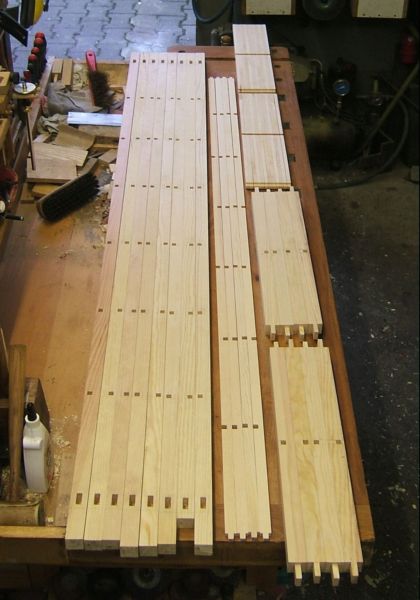
Bild 31
Zusammenstecken der Kumikos:
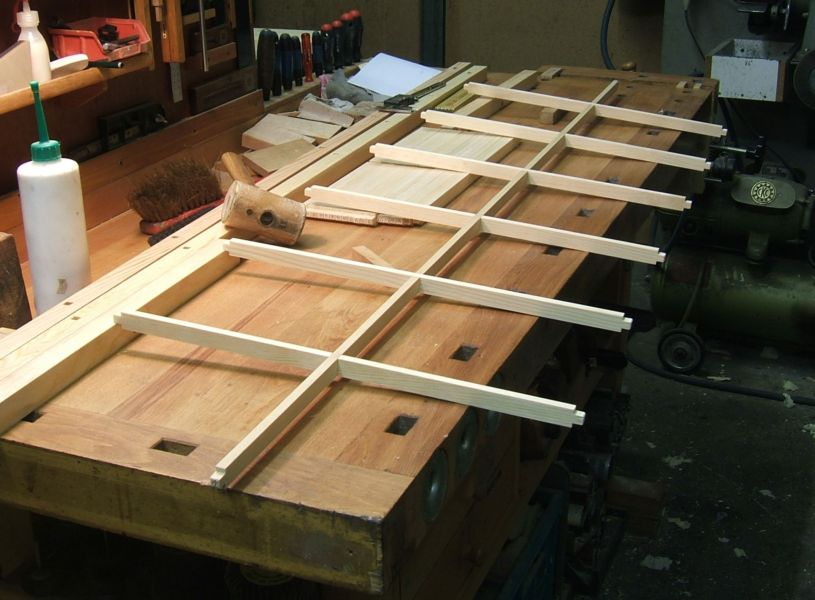
Bild 32
Verleimen des Paravents:
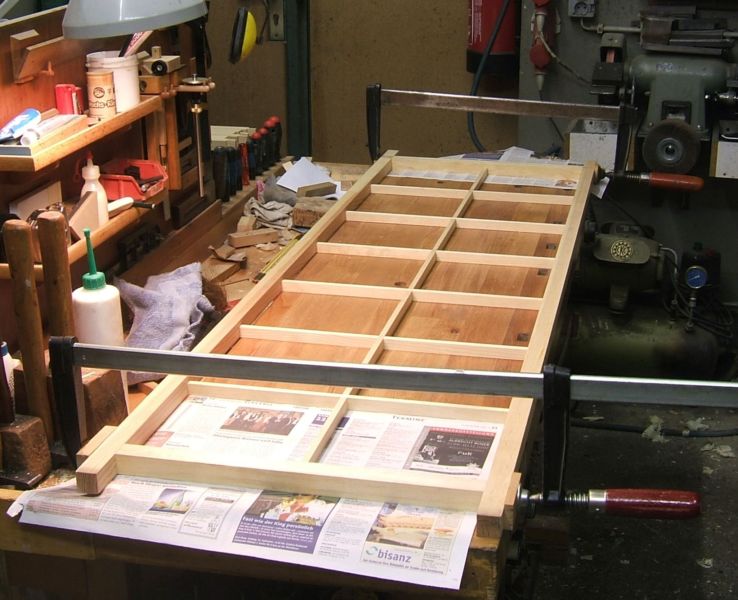
Bild 33
Absägen der oberen Überstände:
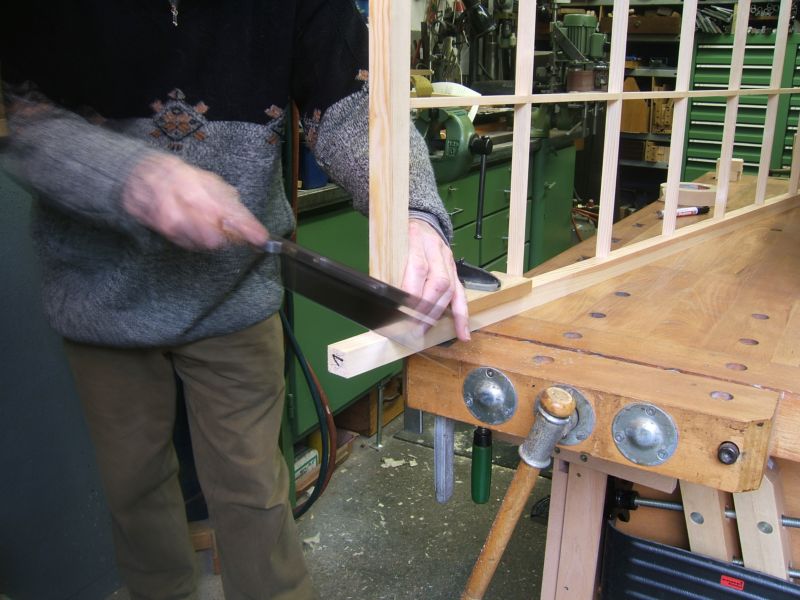
Bild 34
Bündighobeln der vertikalen Rahmenhölzer mit dem Veritas Low Angle Jack Plan auf der Stoßlade:
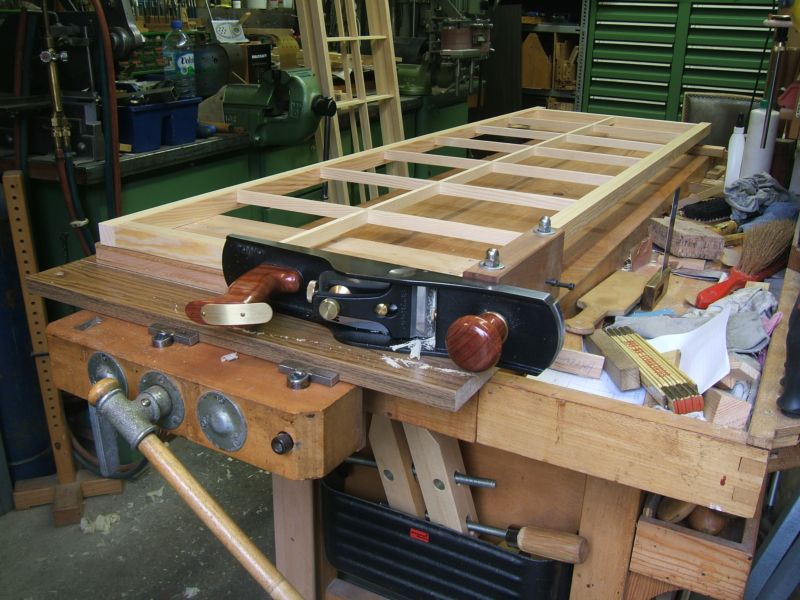
Bild 35
Detailaufnahme der Überblattung und der Verzapfung der Kumikos:
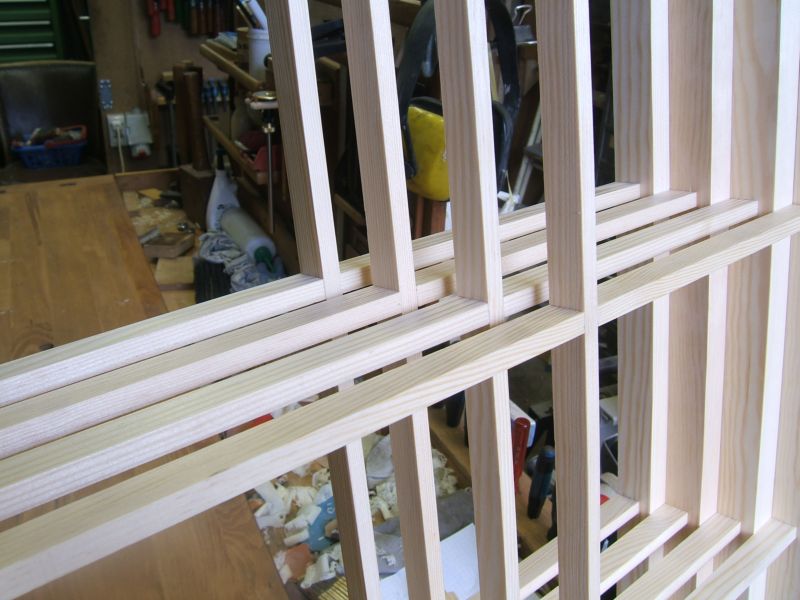
Bild 36
Detailaufnahmen der Rahmenecken. Es war Gott-sei-dank nur minimal mit dem Putzhobel nachzuarbeiten. Alle Rahmen sind im Winkel und nicht windschief!
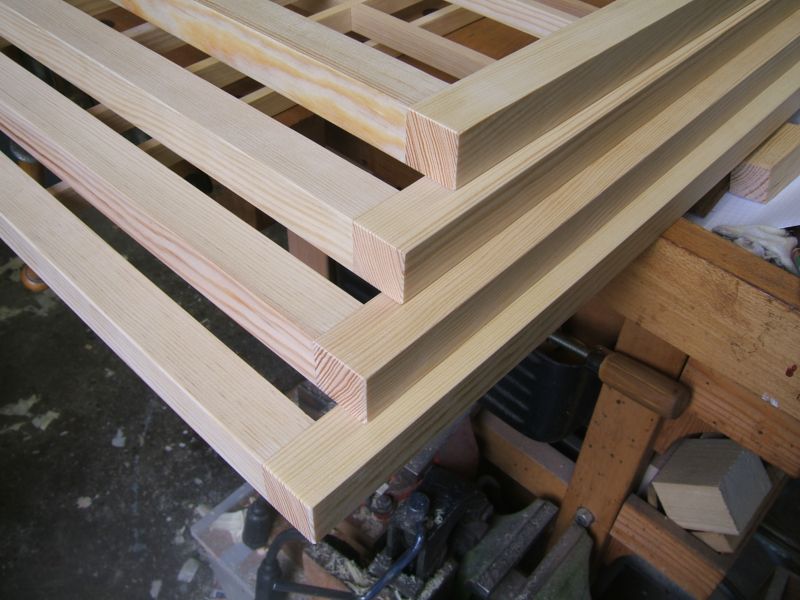
Bild 37
Montieren der Scharniere:
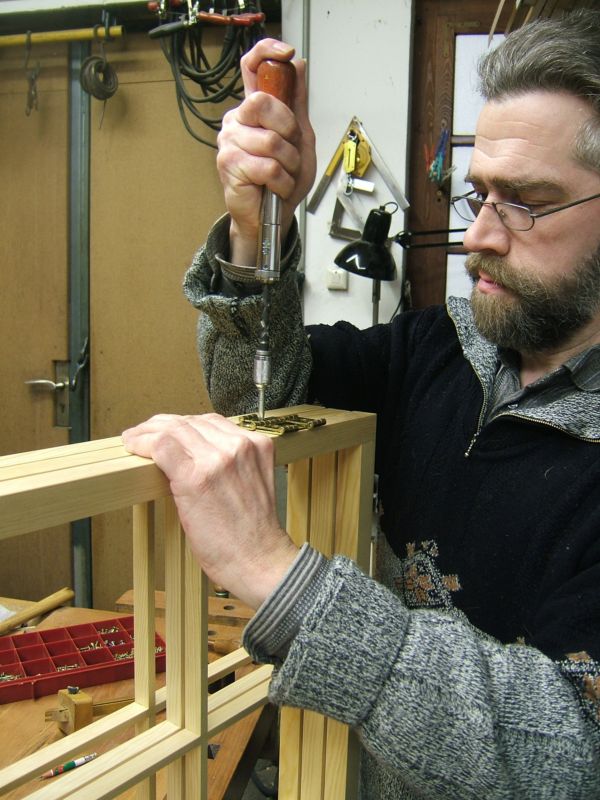
Bild 38
Bespannen des Paravents mit Shoji-Papier:
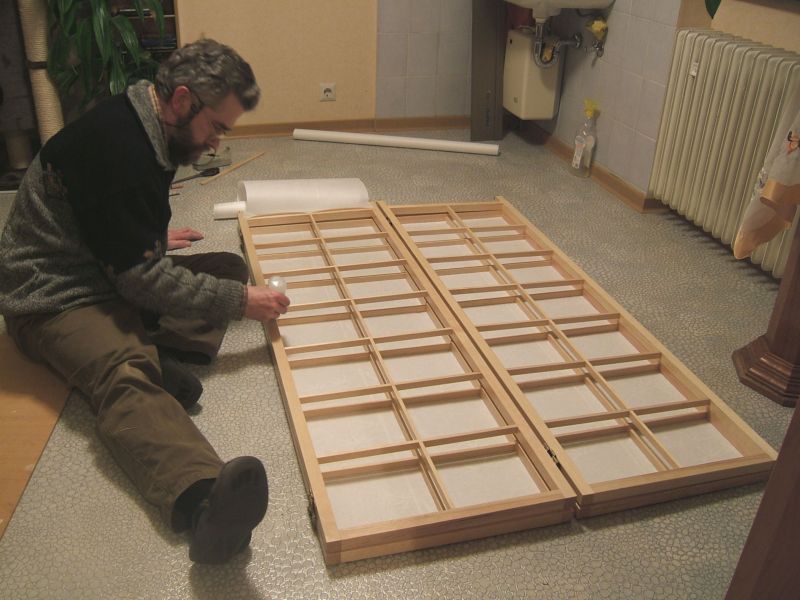
Bild 39
Detailaufnahme der Verklebung und des genialen Scharnieres:
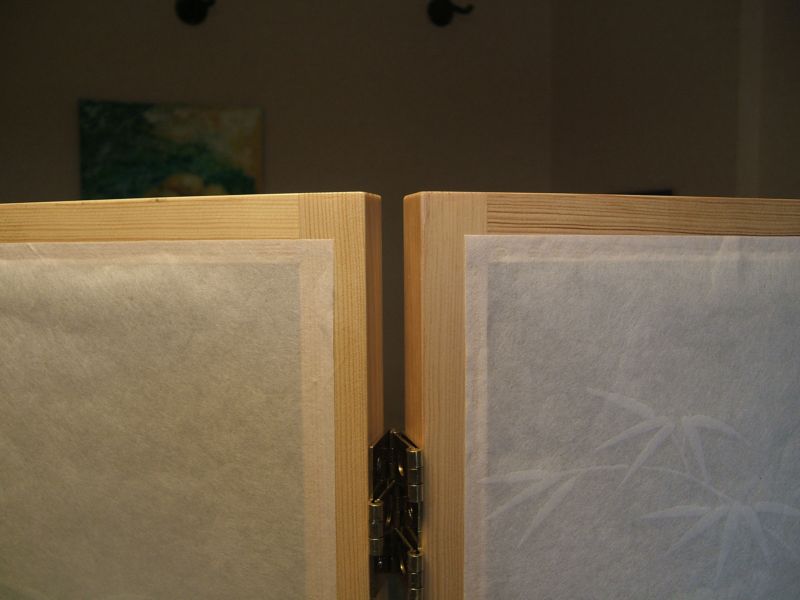
Bild 40
Das gute Stück ist fertig:
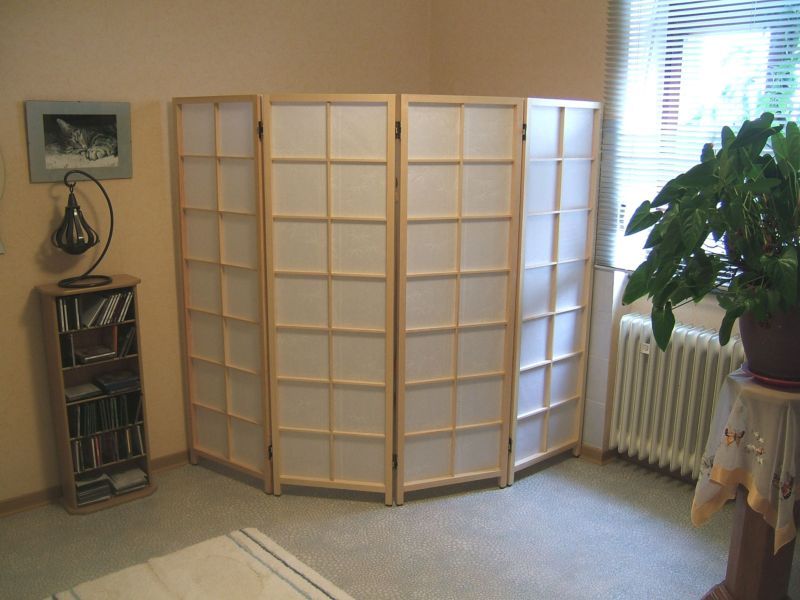
Gruß, Bernhard